Expert Details
Flexible Packaging Materials; Film Extrusion, Extrusion Lamination, Food Packaging, and Food Packaging Safety
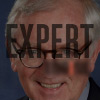
ID: 729658
Georgia, USA
Inductee, Packaging Hall of Fame
Expert has spent over 35 years in the development and application of functional materials for a variety of packaging and non-packaging applications (process and platforms). He has developed various multi-layered barrier films for direct use and for use in laminations. Expert served as the Principle Investigator for a US Department of Defense research study to develop an all-polymeric, high oxygen, water vapor and light barrier materials for thermally-processed low acid canned foods with a 36 month shelf life. He served as the chairman of several professional Flexible Packaging industry groups and has been a frequent organizer of and speaker at industry conferences.
Expert was responsible for the multi-disciplinary team that developed flexible packaging materials, converting processes and manufacturing platform to support a >$10MM product line of packaging materials for fresh cut fruits and vegetables. This involved strategic sourcing, converting machinery modifications, state-of-the art process introduction, customer qualifications, and shelf life studies.
Expert was responsible for all continuing warranties of food contact materials for a >$1b product line. While primary focus was on the US FDA, he developed migration study protocols and GMP practices for EU compliance, as well as other countries. He was a contributing member of the industry group that obtained a US FDA food Contact Notification approval for a set of UV- and EB-energy cured food contact coatings.
Expert managed the introduction and use of vacuum metalized plastic films as functional barrier materials for modified atmosphere packaging of dry, oily foods. He developed base sheets for these uses and pioneered manufacturing of high-volume holographic embossed films with aluminum deposited coatings for flexible packaging applications.
Expert has been responsible for optimizing the use of flexible packaging materials in a variety of form/fill/seal packaging operations.Developed generally recognized as safe/ threshold of regulation documentation for pouch packaging materials with UV-cured overprint intended for dry mix products. Identified appropriate residuals monitoring techniques for food packaging company using recycled fiber.I) Provided Food Safety System Certification Gap analysis for paper converter planning to produce food packaging component.
II) Served as technical adviser to a certified Safe Quality Food auditor during audit a rigid plastic packaging material manufacturer.Provided calculations for estimated daily intake of chemical migrant from new food packaging material component seeking US Food Contact Notification listing.Consulted with major packaging manufacturing equipment OEM regarding good manufacturing practice for food safety aspects of the equipment
Education
Year | Degree | Subject | Institution |
---|---|---|---|
Year: 2004 | Degree: | Subject: Advanced Innovation Management | Institution: Georgia Institute of Technology |
Year: 1989 | Degree: | Subject: Management Development Program | Institution: George State University |
Year: 1979 | Degree: M.B.A. Course Work | Subject: | Institution: Cleveland State University |
Year: 1973 | Degree: MS | Subject: Environmental Studies | Institution: Yale School of Forestry and Environmental Studies |
Year: 1971 | Degree: BA | Subject: Biology and Chemistry- Combined Science | Institution: Yale College |
Work History
Years | Employer | Title | Department |
---|---|---|---|
Years: 2011 to Present | Employer: Undisclosed | Title: Owner | Department: Packaging and FDA |
Responsibilities:Consultant to manufacturers and users of flexible packaging for manufacturing efficiencies, FDA food contact compliance and product development.: Consultant to users and producers of flexible packaging regarding product, process and platform development, intellectual property management and food safety compliance…expert witness regarding flexible packaging for shelf stable low acid canned foods and pouch failure modes; consulted in start-up of MAP food product with Internet distribution channel; identified problem and confirmed solution for package failure from inadequate chemical resistance; prepared validation and verification programs to assure the safety of PCR fiber in paper direct-food-contact packaging; ongoing assessment of FDA compliance of direct-food contact packaging product line. Prepared market assessment of global variation of flexible packaging applications. Frequent publisher and presenter at conferences and webinars of industry and educational groups. Consult regarding Good Manufacturing Practices for safe manufacture of food packaging. |
|||
Years | Employer | Title | Department |
Years: 1981 to 2010 | Employer: Printpack | Title: Director of Product Development | Department: Corporate Development |
Responsibilities:Manged multi-million dollar projects for functional flexible packaging product and process development. Contributed to 20 fold increase in company size during career their.Divisional Vice president of Manufacturing (Applied Physics Research Division) Successful 30 year career focused on product and process development. Efforts contributed to multiple +$10 million product platforms including: 1) extrusion laminated metallized OPP snack food packaging; 2) fully-coextruded forming/nonforming web for frozen boil-in-bag meals; 3) nitrogen flushed vertical form fill seal snack food packaging; 4) modified atmosphere packaging for fresh-cut produce; 5) High MVTR easy-open HDPE blown coex for dried food box liners; 6) High barrier pre-made stand-up pouches. Direct responsibility for inventorying raw material status and certifying domestic and international food safety compliance (US, EU, Canada, China, Indonesia, and others); Developed corporate intellectual property policy and coordinated ongoing activities with patent counsel; represented company at NFS-sponsored Center for Advanced Processing and Processing. Significant roles in corporate interdepartmental planning committees: 1) Corporate Integrated Manufacturing Systems (MRP II) - Directors Committee; 2) Total Quality Management - Steering Committee (Co-chairman, Supplier Certification Subcommittee); 3) Advanced Cost Management System - Client Review Committee; 4) Corporate Growth Policy Committee; 5) Strategic Purchasing Committee; 6) ISO 9001 Policy Committee (Leader, Product Design Subcommittee); 7) Stage-Gate Implementation Committee; 8) M&A Due Diligence Committee (intellectual property responsibility). Principle investigator for dedicated development initiatives: 1) Manufacturing Vice president for wide web; high speed micro-embossed products. Produced a four million square foot commercial order within six months of product’s invention. 2) Conceptualized, organized, and tracked $2.4mm R&D Contract to develop packaging systems for advanced food processes: U.S. DOD -Combat Feeding Directorate). Project managed on time and on budget with commercial results |
|||
Years | Employer | Title | Department |
Years: 1979 to 1981 | Employer: Flexible Packaging Assn. | Title: Technical Director | Department: Development |
Responsibilities:Managed member committees for specifications and test methods; prepared and delivered testimony concerning government regulatory proposals; planned and directed member meetings; represented the industry on committees of government agencies and trade group alliances. |
Government Experience
Years | Agency | Role | Description |
---|---|---|---|
Years: 2008 to 2010 | Agency: US Army Natick Soldier Research, Development and Engineering Center | Role: Principle Investigator | Description: Managed multi-year $3 million project to develop high-barrier polymeric laminations for 3 year shelf life rations. |
International Experience
Years | Country / Region | Summary |
---|---|---|
Years: 1980 to 1980 | Country / Region: Sweden | Summary: He reviewed a high barrier film co-extrusion process. |
Years: 2007 to 2007 | Country / Region: Japan | Summary: Assessed the market potential and manufacturability of several innovative Japanese packaging formats for consideration in US markets. |
Years: 2002 to 2002 | Country / Region: Korea | Summary: Was responsible for reviewing Korean shrink label manufacturing processes (printing and seaming) and returning to his employer with an implementation plan for domestic entry into such markets. |
Years: 1995 to 1995 | Country / Region: Great Britain/Germany | Summary: Was asked to provide a feasibility study of self-manufacture of OPP films for his employer, including review of commercial equipment and pro forma production plans. |
Years: 2011 to 2016 | Country / Region: Philippines | Summary: Provide ongoing technical and shop-floor-control advice to Philippine converter using gravure printing; extrusion/laminating and coating and pouch making processes. Ongoing as of Apr,2013. |
Years: 2011 to 2016 | Country / Region: Korea | Summary: Assist Korean extrusion laminator/coater OEM with technical service for prospects |
Career Accomplishments
Associations / Societies |
---|
PLACE division, TAPPI; Flexible Packaging Division, SPE; RadTech North America. Advisory Committees: UN International Atomic Energy Agency (1 year), USDA National Institute of Food and Agriculture (3 years) |
Licenses / Certifications |
---|
Food Safety Systems Certifications: HACCP Manager and Implementing Safe Quality Foods Systems |
Professional Appointments |
---|
Flexible Packaging Assn.: Chairman, Technical Committee Member, Solid Waste Task Force Product Dev. Mgmt. Assn: Board of Directors, Georgia Chapter Treasurer, Georgia Chapter Society of Plastics Engineers: Chairman, Flexible Packaging Div., Division Board of Directors ASTM: Member F2 (Flexible Barrier Mats.), Member D10 (Packaging) TAPPI: Chairman, Flexible Packaging Comm., Chairman, Technical Program Comm., Winner: Div. Technical Award RadTech North America: Board of Directors, Chairman Eh&S Subcommittee |
Awards / Recognition |
---|
Selected: Fellow (Society of Plastics Engineers) Recipient: Riester-Davis Award for Lifetime Achievement (Food Processing &Packaging Division-Institute of Food Technologists) Panelist Radiation Technology in Development of Advanced Packaging Materials for Food Products”; International Atomic Energy Commission Panelist: USDA National Institute of Food and Agriculture: Improving Food Safety & Improving Food Quality Inductee: National Packaging Hall of Fame (Packaging Machinery Manufacturers Association) Member: Center for Advanced Processing and Packaging Studies (National Science Foundation) Recipient: Zweig Prize for Technical Contributions (Flexible Packaging Division-Technical Association of the Pulp and Paper Industry) |
Publications and Patents Summary |
---|
Expert has contributed to a half dozen food and food packaging books and numerous industry articles and presentations. He recently published a full-length book on a number of packaging techniques, materials and technologies. Peer Reviewed Publications: 1 Books: 1 Book Chapters: 5 |
Additional Experience
Expert Witness Experience |
---|
Provided expert report and deposition testimony on foil and non-foil retort pouch technology. Provided expert report on technical and commercial drivers of QSR condiment packaging Provided expert report and deposition testimony on in-field delamination of flexible package lamination Provided expert report on in-field loss of heat seal (Lidding to APET tray) Provided expert report and deposition testimony on cold-form blister pack for pharmaceutical/medical device use. Provided expert report and court testimony on research, development, and demonstration process for market introduction of advanced polyolefin resins Provided expert report on state of prior art rgarding alleged patent infringement. |
Training / Seminars |
---|
Prepared/presented Webinars on US FDA Food Contact Material Compliance; Good Manufacturing Practices for Food Contact Materials Manufacturers, and US and EU compliant use of printing inks on food packaging. Food Safety Training: Implementing SQF (2013); HAACP Manager (2013): Principles of Internal Auditing (2014), Advanced HACCP (2015) Prerequisite Programs (2016): HACCP for Manufactur-ing Food Packaging Materials (2019) |
Vendor Selection |
---|
Past responsibility for locating best in world oxygen and water vapor barrier films; and complex film co-extrusion lines for development of new products. |
Marketing Experience |
---|
Frequent presenter of technical papers at flexible packaging industry conferences. |
Other Relevant Experience |
---|
Experienced project manager; formerly a certified product development professional; experience teaching graduate level course work in food packaging and product development management. Formal training (with successful teting rsults) for Food Safety Systems Certifications: HACCP Manager and Implementing Safe Quality Foods Systems; advanced HAACP; Internal Auditing. Registered IFS PACSecure GFSI Scope M standard |
Language Skills
Language | Proficiency |
---|---|
French | He is able to read French and converse slowly in the language. |
German | He is able to read German patents and technical literature and analyze relevance to project work. |
Fields of Expertise
flexible packaging laminate, multi-layered packaging material, flexible package, food packaging material, barrier polymer, moisture barrier material, flexible packaging material, perishable food, Food and Drug Administration food packaging regulation, packaging migration, vacuum deposition, retort pouch, viscous material packaging, post-harvest technology, boil-in-bag package, contract manufacturing, food shelf life extension, bag manufacturing, plastics printing, cold seal packaging process, food labeling regulation, microwave susceptor film, ultrasonic sealing, Coalition of Northeastern Governors, primary packaging, frozen food package, food shelf life, microwave food package, Food and Drug Administration CFR-21 part 175, flexible packaging film, polyvinylidene chloride, food packaging equipment, polyester film, food inspection, vacuum deposition equipment, microwave food packaging process, plastic food package, modified atmosphere packaging, phase-change product packaging material, environmentally friendly packaging material, product life cycle, shelf life, food packaging plastic, Food and Drug Administration regulation, food retorting, food safety, food packaging process, food antimicrobial additive, aseptic packaging process